We’re consistently engaged in processes.
That cup of joe you made this morning earlier than diving into your each day duties? A course of.
The onboarding of your newest shopper? A course of.
The price range planning for this quarter? You guessed it; that’s a course of, too.
A workforce’s set of processes dictates what they do, why they do it, and the way. To place it merely, processes are the spine of any workforce. However are your each day processes optimized? Are they meaningfully reviewed often, and is success being measured?
If the reply isn’t any, you want course of optimization.
What’s course of optimization?
Course of optimization is a scientific method to analyzing and enhancing enterprise processes to realize most effectivity, effectiveness, and high quality. It is an ongoing course of of constructing certain your enterprise runs like a well-oiled machine. By constantly figuring out and eliminating inefficiencies, you’ll be able to enhance productiveness and achieve a aggressive edge.
The excellent news is that it is not a handbook course of. Instruments like enterprise course of administration software program can outline and automate this optimization course of for you. You may get an summary of your organization and slim it right down to departments needing essentially the most assist.
Earlier than discussing course of optimization intimately, it’s important to know how the phrase “course of” is outlined absolutely.
What’s a course of?
The Oxford English Dictionary (OED) defines a course of as “a collection of actions or steps taken to realize a specific finish.”
Going again to the sooner instance of constructing espresso, that course of began with you both grabbing a mug out of the cabinet or making ready the boiling water. By the top of it, you would get pleasure from a cup of espresso and begin the day without work on the fitting foot. It was a set of duties you wanted to hold out to get what you wished (or, relying in your caffeine compulsion, wanted).
There are numerous methods to regulate any given course of in order that it’s objectively higher, from eliminating sure duties to including new ones, rewriting a specific step within the course of, or reordering the method’s order of duties to enhance the general circulate. Both approach, course of optimization goals to make enterprise operations extra environment friendly, simpler, and simpler, time-consuming, and wasteful.
Kinds of course of optimization strategies
There are a number of completely different methodologies and instruments used for course of optimization, every with its personal strengths and purposes. Listed here are among the most typical varieties:
1. Six sigma
This data-driven method focuses on minimizing defects and variations in a course of. It makes use of statistical evaluation to establish and remove root causes of issues, aiming for an extremely low defect charge (lower than 3.4 defects per million alternatives). It follows a DMAIC cycle: outline, measure, analyze, enhance, and management.
2. Lean manufacturing
Lean manufacturing originated within the auto business and focuses on eliminating waste and maximizing course of worth. It emphasizes steady enchancment and streamlining workflows to scale back lead occasions, enhance high quality, and reduce prices. Lean rules will be utilized to any course of, not simply manufacturing.
3. Whole high quality administration
Whole high quality administration (TQM) is a customer-centric method to course of optimization that focuses on steady enchancment all through all areas of a enterprise. It includes all staff within the course of enchancment effort and emphasizes assembly buyer wants and expectations.
4. Enterprise course of administration
Enterprise course of administration (BPM) is a well-liked and holistic method to course of optimization that includes figuring out, modeling, analyzing, and enhancing enterprise processes. It offers a framework for managing and optimizing processes throughout a whole group.
5. Steady enchancment (Kaizen)
Kaizen is a Japanese philosophy that emphasizes steady enchancment. It is primarily based on the concept small, incremental adjustments can result in vital enhancements over time. Kaizen encourages all staff to establish and recommend methods to enhance their work processes.
6. Course of mapping
Course of mapping is visually useful for documenting and analyzing processes. It includes making a flowchart or diagram that exhibits all of the steps concerned in a course of, in addition to the choice factors and handoffs. Course of mapping instruments may help establish bottlenecks, redundancies, and alternatives for enchancment.
7. Course of mining
Course of mining instruments use information to extract information about real-world processes. It might establish inefficiencies, variations, and bottlenecks in a course of and assist enhance the accuracy and completeness of course of maps.
Easy methods to do enterprise course of optimization your self
Earlier than we get into the nuts and bolts of present process course of optimization, here is a query: are you apprehensive about how lengthy course of optimization will take?
In that case, don’t be.
Enterprise course of optimization doesn’t should be time-consuming, taking hours and hours out of your already busy schedule. All you need to do is dip into course of optimization each quarter to revolutionize your processes! Plus, follow makes excellent; you’ll do it faster every time.
Now, for those who underwent Six Sigma Black Belt coaching and wished to make use of a myriad of Six Sigma instruments reminiscent of course of mining, FMEA, and worth stream mapping, that’s when course of optimization would take a considerably bigger period of time. To get the very best of each worlds – going about course of optimization in a Six Sigma-approved method in essentially the most time-efficient approach potential – you’ll wish to observe the DMAIC methodology.
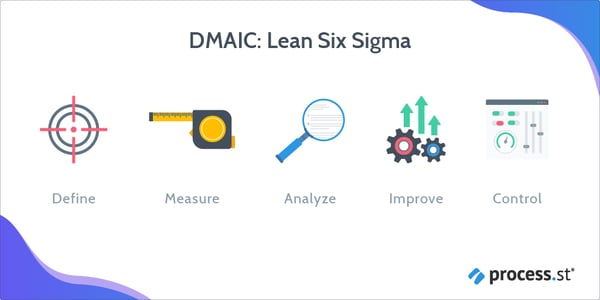
I’m about to elucidate the DMAIC technique within the following 6 steps so you’ll be able to optimize your processes correctly.
1. Guarantee processes are documented
For DMAIC to work—and for any course of optimization technique, technique, or course of to work—you’ll have to have documented your processes first.
Enterprise processes will be documented with widely-known applications reminiscent of Google Docs and even Microsoft Excel, however contemplating the plethora of software program on the market, reminiscent of BPM software program, that makes documenting, utilizing, optimizing, and managing your processes a breeze, choosing a purpose-built device is price your whereas.
However what’s most essential right here is getting your processes down, detailed, and documented. In any case, you’ll be able to’t truly optimize your processes for those who can’t bodily see how they work, what’s concerned, and what the present iteration of every course of is.
Not solely is documenting your processes integral for DMAIC and course of enchancment however there are a ton of added on a regular basis pluses that come from doing so.
As an illustration, suppose again to earlier once I mentioned how optimized processes could make onboarding, particularly, sooner and higher. When the onboarded rent begins enterprise the identical work-related processes and duties as their colleagues, they’ll become familiar with every part if there are documented processes to observe and the directions for what do merely haven’t been handed down by worth-of-mouth.
Equally, let’s say a special worker can’t bear in mind a sure step of a course of. As a substitute of asking their supervisor what to do (and thereby distracting the supervisor from no matter they’re engaged on), the unsure worker can refer again to the documented course of. It’ll refresh their reminiscence, scale back any nervousness they might have had, and immediate them to do what must be completed!
Evidently, documented processes aren’t simply downright helpful — they’re essential.
2. Outline which course of must be optimized
As soon as enterprise processes have been sufficiently documented, it’s time to begin DMAIC itself and outline which course of you’ll optimize first.
To start with, it could appear somewhat overwhelming – particularly contemplating there are probably tens, a whole lot, or even perhaps hundreds of processes to optimize. That’s why it’s finest to create an inventory of key processes to optimize after which work your approach down the checklist.
To determine this checklist, ask your self:
- Which processes are used most continuously? Particularly, what number of days per week? What number of occasions a day? By what number of workforce members?
- What processes have the very best output? That’s, which processes have finish objectives which are essentially the most essential for the enterprise to not simply keep afloat however thrive?
- Which processes have the very best ROI? Which processes are you getting essentially the most monetary profit from as soon as they’ve been accomplished?
- Which may contribute to ROI development if improved? Which processes, if optimized, may grow to be a few of your most essential, most helpful processes with regards to producing ROI?
Do remember the fact that, to keep away from overload and scrambling your mind, you’ll wish to optimize your processes one after the other. In any other case, preserving on prime of a number of processes may show tough and will trigger you to make errors and do additional harm to your enterprise processes.
When you’ve created your checklist, the method on the very prime—be it onboarding purchasers or making a venture administration plan—is the one you’ll be optimizing first, so outline it: Write down the title of the method, its aim, the way it begins and ends, who it includes, and what it includes. Present your self and others you’re working with with the method’s primary however important data.
3. Measure how the method performs
Information is on the coronary heart of DMAIC, so it’s solely proper that you just measure how the method is faring early on. This offers a benchmark for a way the method is working earlier than any adjustments are applied. Fortunately, measuring a course of isn’t as onerous because it sounds.
First, you’ll want to collect quantitative information. This could simply be completed by measuring the method towards its KPIs (you need to have already got 2-3 KPIs per goal). In case you don’t have any key efficiency indicators for this, nonetheless, take into consideration the anticipated outputs of the method in query: is the method attaining these outputs as supposed? Is it doing so in an applicable timeframe? Is it failing to fulfill anticipated outputs in any respect? Principally, that is the purpose the place you’ll wish to contemplate the method in a important approach, backed up with quantifiable information.
Then, it’s time for qualitative information. Gathering qualitative information is way much less daunting than it sounds, too. As an illustration, one simple approach of getting the info you want is to ask customers and/or the method proprietor how they really feel it performs. They are able to instantly let you know what it’s like to make use of the method continuously, what any points are, and whether or not or not it’s profitable as a course of.
After measuring the method’ efficiency, maintain all of the details and figures you’ve obtained someplace protected (learn: don’t write them on paper that’ll inevitably go walkabout and by no means be seen once more—use a correct resolution for documenting data).
4. Analyze how it may be optimized
Within the final half – the measurement step – you discovered good information on how the method is performing with out doing any first-hand checks your self. However that’ll now change with this evaluation step, because it’s right here the place you and anybody you’re working with will run by way of the method.
As you run by way of the method with an analytical, important eye, you’ll naturally discover the place the method isn’t pretty much as good appropriately. However seeing as you’re a first-timer with regards to course of optimization and DMAIC, that will help you out, listed below are some pointers for what to contemplate and analyze:
- How lengthy does it take to finish the method? Is it in an applicable timeframe? Is it slower or sooner than anticipated?
- The place do bottlenecks happen? If the method is a multi-person course of, is there a degree the place one member of employees can’t proceed with their duties as a result of any person else is taking too lengthy to finish theirs?
- Are any steps complicated or written in a bewildering approach, inflicting the method person to carry out duties poorly or to skip them outright?
- Are there any wasteful steps? Usually known as “Muda”—the Japanese for ‘waste’—in Six Sigma circles, wasteful steps end in any one of many seven types of Muda (waste of overproduction, waste of time readily available, waste of transportation, waste of processing itself, waste of inventory at hand, waste of motion, and waste of constructing faulty merchandise). Are these wasteful steps and duties current in your course of?
- Can components of the method be automated? Automation is an excellent, forward-thinking approach of optimizing a course of. McKinsey even found that 45% of actions can simply be automated with present know-how. All you must get began is to combine one device—let’s say CRM software program—with one other with webhooks, API, and even with a third-party device that integrates separate apps for you.
5. Enhance the method
The penultimate stage of DMAIC – enchancment – is all about performing on the info, data, and perception you’ve gathered within the earlier steps and making useful course of adjustments.
One elementary piece of recommendation I’ve is to check the adjustments earlier than you implement them. By testing them beforehand, you’ll affirm whether or not the adjustments you suppose you need to make will truly profit the method in query.
Seeing as you’ve documented the method you’re optimizing, testing the adjustments is simple. Simply make a duplicate of the documented course of, alter it as essential, after which get the standard course of customers to observe the method with the adjustments.
As soon as they’ve completed so, collect their suggestions to see whether or not the changes have had a constructive impression or not. With the adjustments that have been deemed as a hit, you’ll wish to deploy, deploy, deploy!
6. Management future course of efficiency
Management is the final a part of DMAIC. Consider it as the purpose the place you’ll tie up any free knots, talk with others in regards to the course of adjustments, and guarantee your now-optimized course of is measured correctly going ahead.
When it comes to tying up free knots, do you must get anyone else’s approval earlier than unleashing the optimized course of and having everybody observe it? In that case, ship the documented course of their approach. Whereas it could take somewhat extra time if they arrive again with extra ideas or concepts, it’s an additional high quality administration step, which is undeniably useful.
Then, you’ll wish to let customers of the method know what’s occurred, why the method has been modified, and reply any questions in regards to the up to date course of. In case you don’t inform course of customers in regards to the updates you’ve made, not solely will they be shocked, however they may determine, out of pure confusion, to not observe up to date steps correctly. This may undo on a regular basis and energy you place into course of optimization within the first place.
To make sure the method is measured and performs effectively going ahead, a easy approach is to bear course of optimization once more within the subsequent quarter. Then, you’ll have the ability to enhance upon the method (if any enhancements will be made). There will likely be situations when no additional enhancements will be made, which the measure and evaluation steps will let about. Both approach, for true course of optimization and management, often reviewing and optimizing the processes is a should.
Now, give your self a high-five – you’ve accomplished the DMAIC steps for course of optimization!
Advantages of course of optimization
So long as there’s a dedication to optimizing your workforce’s enterprise processes correctly and often, then you definately’ll open your workforce as much as an entire host of business-changing advantages.
Elevated productiveness
Workers received’t simply full their processes sooner, however their output will yield stronger outcomes, too. For example, let’s say a member of the gross sales workforce is onboarding a brand new rent, they usually’re following an onboarding course of that’s lately been optimized. By taking out the unique steps that resulted in bottlenecks, the brand new rent will be educated up sooner, which means they’re capable of get straight into doing good work, which you’ll then reap the monetary advantages of!
Lowered error
If a course of hasn’t been critically examined, there might be steps that actively trigger the particular person following it to hold out a process they shouldn’t or to do it in a approach they now not ought to. However by frequently reviewing, optimizing, and updating your enterprise processes, inconsistencies and inaccuracies that result in error are fully eliminated.
Extra agility
Within the up to date world of enterprise, performing slowly doesn’t reduce the mustard. Agility, as an alternative, is essential; you must change and adapt consistently. Agile groups have a better probability of being within the prime quartile with regards to organizational well being (group well being, for those who don’t already know, is an indicator of long-term excessive efficiency). Fortunately, the very nature of present process course of optimization often means you’re enabling your processes—and your workforce at giant—to be extra agile.
Set up and additional a tradition of processes
To have a tradition of processes, you should take your enterprise processes critically, making certain they’re documented, extensively used, and optimized over time. Optimizing your enterprise processes is an undeniably essential a part of establishing after which furthering a tradition of processes inside your workforce.
Improved bottom-line
Let’s reduce to the chase: the enhancements made to processes as a part of course of optimization have a direct, constructive impression on your enterprise’s backside line.
Whereas these advantages will certainly get keen workforce leaders occupied with course of optimization, the actual driving drive for present process course of optimization must be that not taking good care of enterprise processes causes harm. From utilizing weak, clunky processes each single day to having all staff unknowingly waste essential effort and time, doing nothing about your outdated, unoptimized processes can drag your entire enterprise down.
Course of optimization, then, is about bettering enterprise processes. But it surely’s about hurt discount, too.
Challenges of course of optimization
Whereas course of optimization gives vital advantages, implementing it successfully will be powerful. By being conscious of its challenges and taking steps to mitigate them, you’ll be able to enhance your probabilities of efficiently optimizing your processes and reaping the rewards of improved effectivity and effectiveness.
- Resistance to alter: Persons are usually creatures of behavior, and any adjustments to acquainted workflows will be met with resistance. This may be attributable to concern of the unknown, considerations about job safety, or just a dislike for disruption.
- Lack of assets: Course of optimization will be resource-intensive, requiring time, effort, and typically monetary funding in new applied sciences or coaching. This is usually a problem for organizations with restricted assets.
- Inaccurate information: Information is crucial for figuring out inefficiencies and measuring the success of optimization efforts. Nonetheless, inaccurate or incomplete information can result in poor decision-making.
- Lack of management buy-in: Course of optimization initiatives can flounder with out the assist of management. Government buy-in is essential for securing assets, overcoming resistance to alter, and making certain the venture’s long-term success.
- Unexpected penalties: Typically, adjustments applied throughout course of optimization can have unintended penalties. For instance, streamlining a course of may result in a decline in high quality, or automating duties may create job redundancies.
- Quick-term focus: Course of optimization is an ongoing course of, not a one-time repair. Organizations that focus solely on short-term beneficial properties might miss out on the long-term advantages of steady enchancment.
- Neglecting the human aspect: Folks perform processes, so it is essential to contemplate the human component throughout optimization. Failing to contain staff within the course of or neglecting their wants can result in resistance and hinder the initiative’s success.
Transferring ahead as a process-oriented firm
By studying by way of and following the directions given on this put up, you’ve set your self up for achievement by changing into a process-orientated firm.
Particularly, you’ve found simply how essential stable processes are in your each day operations – to not point out your backside line – and also you’ve documented your integral enterprise processes. Most noteworthy, although, is that you just’ve began to make your approach by way of the processes, optimizing and enhancing them step-by-step!
With this new-found tradition of processes, right here’s to doing the very best work potential, boosting workforce collaboration, and boosting productiveness. Plus, for those who ever determine—or are required—to begin utilizing high quality administration programs reminiscent of ISO 9001, the endeavor will likely be painless.
Time to outrun the group
Processes are the spine of your workforce, and the processes they bear day-after-day decide their total success. Not enhancing and optimizing continuously used, important processes are actively turning down the chance to work higher, sooner, and extra intelligently. In reality, outdated and inefficient processes waste practically a 3rd of staff’ time every working day.
By following the DMAIC technique for course of enchancment outlined above, you may get and maintain your processes in examine—all the time. To make sure that course of optimization—along with documenting, utilizing, and managing your processes—stays plain crusing, you’ll wish to make the most of a devoted BPM device.
Make the very best use of workflow automation to boost your enterprise’s each day productiveness ranges.
This text was initially printed in 2020. It has been up to date with new data.