When constructing a giant-scale airplane, you don’t need any guesswork together with your linkages. The all-important connections between our servo and the management surfaces are completely tied to the size of our plane’s lifespan. There are a number of frequent linkage strategies. You need to use a strong pushrod of a reasonably quick size for a direct management setup and, for longer distances, you should utilize a inflexible carbon tube or insert a versatile pushrod right into a information sleeve braced securely inside the fuselage for exact management. One other well-liked setup is to make use of a pull-pull system, which is quite common for rudders on giant-scale aerobatic fashions at any time when the rudder servo is positioned near the cockpit space. Whichever technique you favor, the set up of those programs have to be finished correctly to make sure the most effective outcomes.
SERVO BASICS
On your management system to work correctly, you need to use the right servo for a given job. Many plane producers provide servo measurement and sort recommendations, and it’s at all times a good suggestion to make use of their suggestions. Servos with 200 oz.-in. of torque (or extra) are perfect for giant-scale plane use—particularly in relation to 3D aerobatic designs. A number of servos are generally used to maneuver a single particular management floor. Be mindful, although, that the quantity of torque actually will depend on the kind of airplane you’re flying. Whereas the 200 oz.-in. instance works nicely for many scale purposes as much as a couple of 130-inch wingspan, it won’t be sufficient for a equally sized aerobatic mannequin the place you simply can’t have sufficient servo torque.
Typically, to realize giant management floor deflections, you possibly can set up an extended servo arm on the servo. Nevertheless, you should definitely additionally maximize the adjustable journey quantity operate in your radio. Whereas having low adjustable journey quantity and lengthy servo arms can produce giant management throws, it’s going to additionally trigger poor mechanical benefit, leading to flutter and probably management floor blow-back throughout flight. Blow-back happens when the management floor can’t deflect the identical quantity within the air because it does on the bottom, and each flutter and excessive instances of blow-back could be deadly to your airplane. Additionally, it’s best to keep away from a number of bellcranks and to maintain the management linkage system so simple as attainable.
MECHANICAL ADVANTAGE
The mechanical benefit that the servo can exert on a management floor is essential. As a rule, whereas maximizing the adjustable journey quantity values, the gap from the servo arm’s heart screw to the attachment level of the linkage on the arm ought to be the identical as the gap from the hinge centerline (pivot level) to the linkage attachment level on the management horn. For instance, if you happen to’re utilizing a 1.5-inch servo arm and the linkage is connected to the servo arm roughly 1.5 inches from the servo screw, then the linkage connected to the management horn ought to be the identical distance (when measured from the hinge line). This precept applies to each “push-pull” and “pull-pull” programs. Utilizing a shorter management horn to extend management floor deflection drastically reduces the servo’s leverage and can lead to flutter.
The upper the adjustable journey quantity share, the upper the servo decision might be. Lowering adjustable journey quantity share will decrease servo decision, which is very undesirable.
PUSH-PULL CONTROL
A “push-pull” management system merely signifies that a servo is related to a single management horn on the management floor. With giant-scale plane, the pushrod have to be inflexible. Most big aerobatic fashions function externally mounted servos which might be related to the management floor with pretty quick titanium rods. For brief linkages (as much as 5 inches in size), Hangar 9 affords Titanium Professional-Hyperlinks which have 4-40 threads to simply accept both a ball-link or swivel-link at every finish. For servos mounted a higher distance away from the management floor, pushrod helps are a should!
The place a pushrod runs the size of the fuselage, you should utilize a fiberglass arrow shaft or a carbon-fiber tube. The pushrod does flex a short time underneath flight hundreds, so helps have to be positioned at a number of factors alongside the pushrod’s size. Exactly positioned holes in a number of formers may also function guides to attenuate the quantity of aspect flex, which may trigger linkage binding.
PULL-PULL DEFINED
It’s fairly frequent to make use of a pull-pull cable system in plane which might be vulnerable to tail-heaviness. This technique is loads lighter in comparison with a pushrod setup of the identical size. Cable guides aren’t typically wanted and should solely be wanted if the cable interferes with the airframe construction. Pull-pull programs are closed-circuit setups. There are two attachment factors on the servo and on the management floor. The cables at all times stay the identical size, so relative to their pivot factors, the geometry of the management horns and the servo arm should stay the identical. If they don’t seem to be, when the servo strikes, the cables will slacken and/or tighten as they transmit the movement to the management floor.
If the management horn on the management floor isn’t aligned correctly with the hinge pivot level, an offset servo arm might be wanted. The quantity of offset within the arm, when measured from the servo arm screw to the attachment factors on the arm, have to be equal to the offset distance on the management horns.
Nylon-coated, braided metal cable is the only option for pull-pull programs, and it’s obtainable from RC corporations like Du-Bro. You can even discover braided cable at most fishing provide shops focusing on deep-sea fishing. Known as “metal chief cable,” it’s nylon-coated and obtainable in a number of thicknesses—0.032-inch (1/32 inch) works nice for giant-scale airplanes.
To connect the cable, a full servo arm or a bell-crank can be utilized. A ball-link clevis is connected to each ends of the servo arm, or bell-crank, the place a threaded rod that has a gap drilled in it to simply accept the cable connection might be threaded into the ball-link. Utilizing a ball-link and a threaded rod is a should so the strain of the cables are adjustable. Over time, the cables might stretch to some extent. If this happens, it’s essential to tighten the cables in order that they’re taut for exact management.
To attach the cable at every finish, slip a ferrule onto the cable and pull the cable by way of the outlet, letting not less than eight inches prolong previous the outlet. Utilizing your fingers, bend the cable right into a slight V the place it passes the outlet and slip the tip of the cable by way of the ferrule. Push the ferrule a couple of 1/4-inch from the threaded rod and gap that the cable is handed into, and loop the cable across the ferrule as soon as extra. When glad, crimp the ferrule in between two to 3 spots, and minimize off the surplus wire. Repeat this course of for the control-horn finish of the set up.
CABLE AND PUSHROD ATTACHMENT
Don’t use Z-bends on the ends of your pushrod wires to connect them to your servo arms. As a substitute, use both a 4-40-size brass clevis or a ball-link clevis. Heavy-duty {hardware} ensures correct management linkages that may face up to the flight hundreds exerted on an enormous airplane. Sullivan Merchandise and Du-Bro Merchandise make steel clevises that may both thread onto a pushrod wire finish with a jam nut or could be soldered into place.
It’s best to have a soldered clevis on one finish of a pushrod and a threaded clevis on the opposite. If you happen to use two threaded clevises, vibration could cause the pushrod to unscrew itself from the clevises throughout flight and that’s by no means an excellent factor.
Heavy-duty ball hyperlinks are additionally a superb method to make the connections. Ball-links guarantee slop-free motion between pushrods and the servo arms, and are perfect for the place there’s a slight misalignment within the total geometry of the linkage. Once more, the right measurement for large scale is 4-40.
Biplane Linkages
Large-scale biplanes pose an fascinating downside as a result of if a separate servo isn’t used for every aileron, it’s essential to hyperlink the higher and decrease ailerons to at least one one other with a linkage. Doing so correctly will lead to the identical deflection on all ailerons. Nevertheless, if this isn’t finished appropriately, all ailerons might have completely different deflection quantities. If you happen to set up a linkage between the higher and decrease aileron, it’s essential to join the pushrod on the similar vertical place on each high and backside ailerons. That’s, if the connector pin is above the trailing edge on the underside aileron, then the connector pin must be equally above the trailing edge on the highest aileron. If this rule isn’t adopted, differential between ailerons will exist. Du-Bro Merchandise additionally affords a big number of pushrod sizes—as much as 30 inches in size. These pushrods transfer forwards and backwards inside plastic or carbon information tubes, which additionally have to be supported inside the fuselage. There are a number of methods to attach the 4-40 threaded wire ends to the pushrod so the pushrod can hook up with the servo arm and management horn. You are able to do it with industrial pushrod adaptors or by threading the threaded wire right into a wooden plug and gluing into the ends of the pushrod tube.
FINAL THOUGHTS
Though many management strategies can be found, it’s best to learn the instruction manuals offered together with your plane and use the producer’s suggestions whereas organising your mannequin. If you happen to’re unfamiliar with the linkage technique, seek the advice of an skilled modeler who has constructed and flown big airplanes with success. A fast tech dialog may save your airframe!

Proven right here is an offset arm that’s related through a pull-pull system to the rudder management horn, which can also be offset from the hinge line.
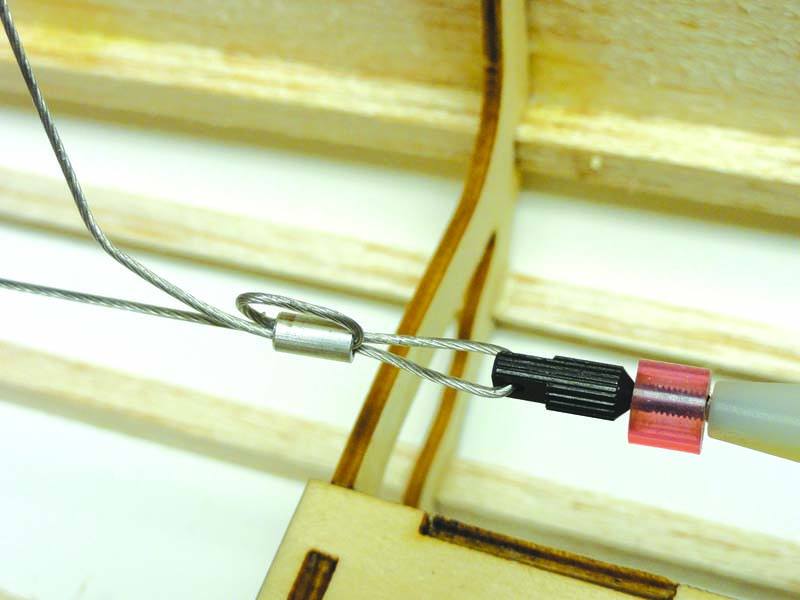
Looping the pull-pull cable by way of the ferrule ensures that the cable won’t pull unfastened after it’s crimped in place.
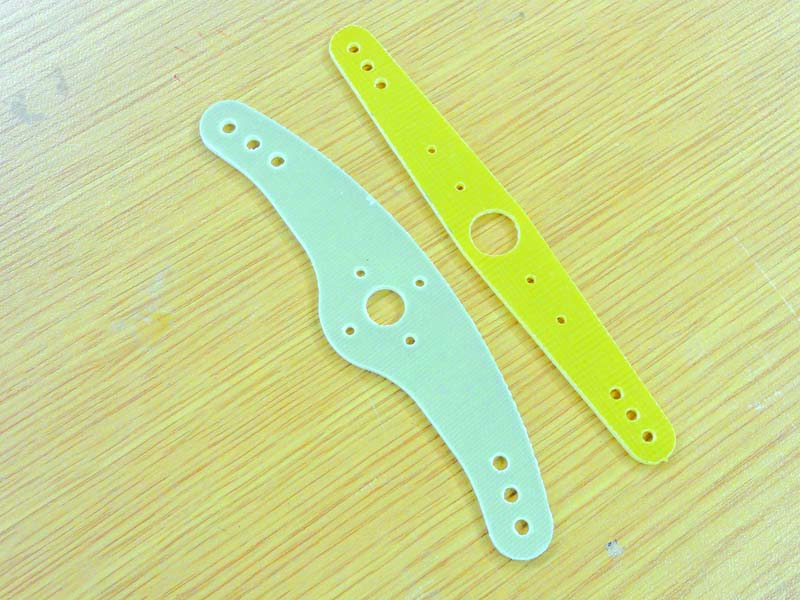
An offset arm in addition to a straight arm for pull-pull. Utilizing a straight arm is helpful at any time when the management horn on the management floor is straight in keeping with the hinge-line. Each arms proven above are to be bolted to a typical plastic or steel servo arm earlier than being secured to the servo.
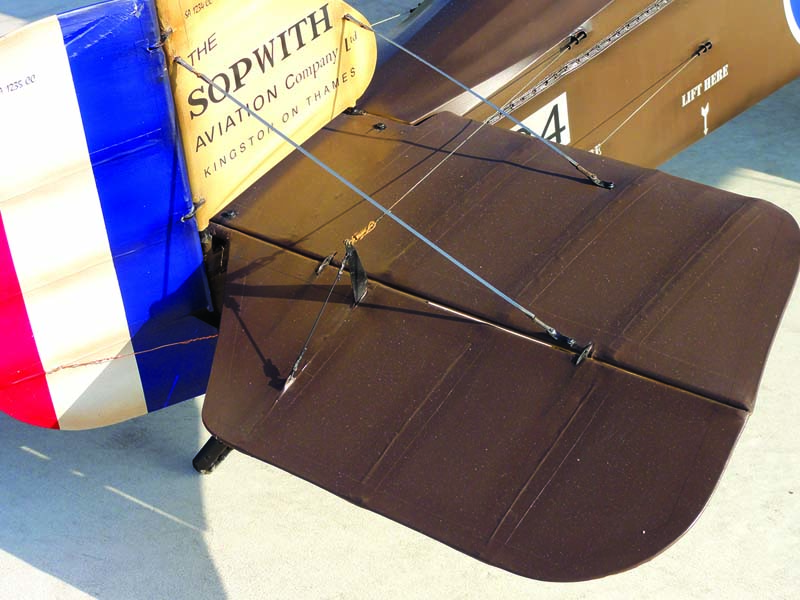
Pull-pull is frequent amongst WW I and different classic plane. Proven here’s a pull-pull system to manage the elevator of this beautiful Sopwith Pup.
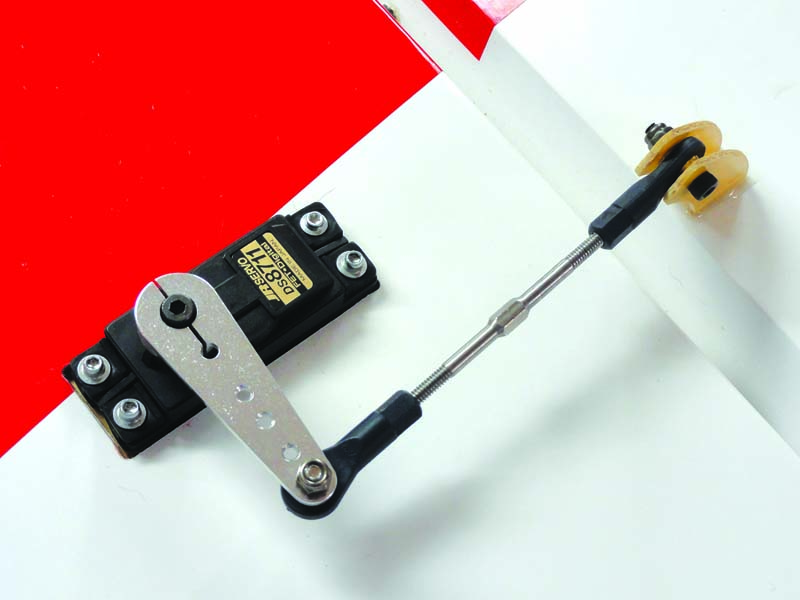
This Hangar 9 Titanium Professional-Hyperlink can prolong to a most size of 5 inches and is reasonably handy at any time when a servo is mounted near the management floor.
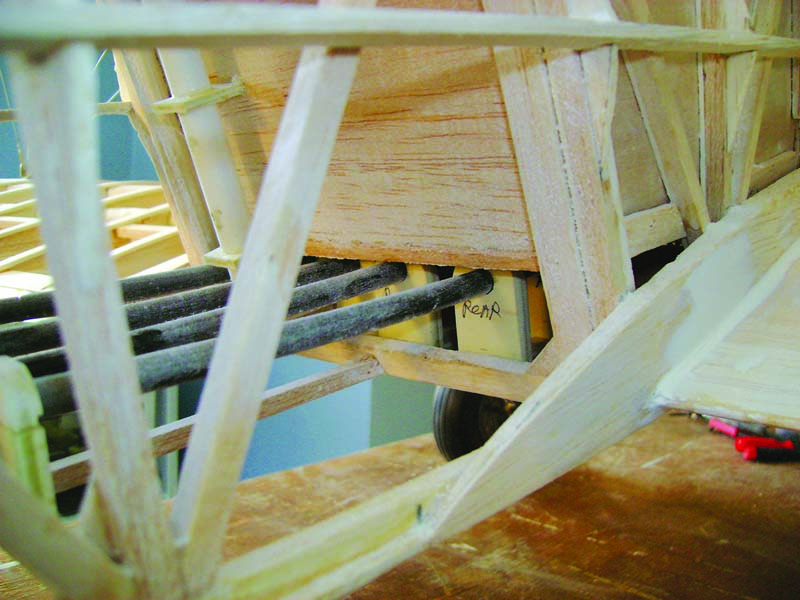
Helps are wanted for pushrods that run nearly the whole size of the fuselage. (Photograph by Raymond Schmidt)
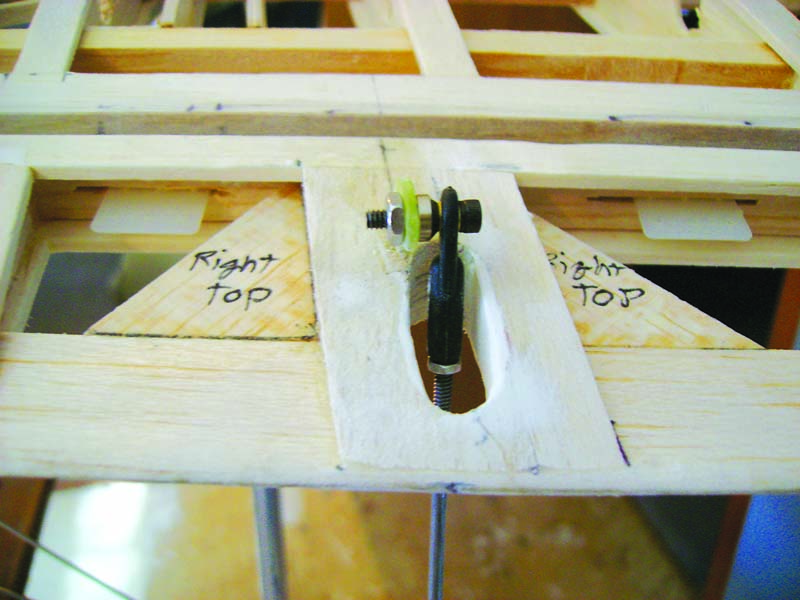
The higher aileron of a giant-scale biplane must be correctly linked to the decrease aileron.
By John Glezellis